My Taylorcraft
restoration project, G-BREY
Page 5, May 2004 - Feb 2005
Go to page 1 2 3 4 5 6 7 8
by Robert Lees
Click on the thumbnails to
enlarge, use the browser's Back button to go back.
May and June 2004 Wing work
commences:
 |
 |
The fuselage gets taken away for storage, and
the wings come out of storage and are delivered to my house. |
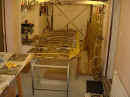 |
It's a tight squeeze... |
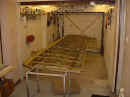 |
...but better after I relocate the other wing
to the living room. |
 |
 |
 |
I had previously removed the butt fittings
(front and rear spars) to inspect and measure them. Note in the left photo the
severe corrosion (painted over) on the rear fitting, so much so that someone decided to
add a doubler to take the loads. A real wasp's nest! |
 |
 |
The magnesium aileron brackets are removed and
disassembled for inspection. These can be prone to dissimilar metal corrosion
between the magnesium and the steel end fittings.
The right-hand photo shows removal of the oilite bushings, using the same drift as
used on the tailfeather bushings. |
 |
Wing aileron bracket after bead blasting.... |
 |
...and after Magna-Dyning. Next step is
etch-prime and then epoxy prime. |
 |
The four other aileron brackets |
 |
Using a cycle spoke key to undo the
wing bracing wires (No.10 slot seems to work great). |
 |
Removal of those pesky, corroded slotted screws
is simplified with the use of a small right-angled screwdriver, upon which pressure can be
borne to keep the blade from "camming out". I cleaned out the slot of each
screw beforehand with a mini hacksaw blade. |
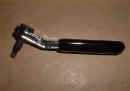 |
 |
The little fibre components inside the wing get
a clean-up...removal of decades of grime, paint and varnish; they turn out like new. |
 |
Some of the threaded end fittings of the wing
bracing wires are of different sizes....any explanations forthcoming? |
 |
..and the compression strut shims also show
minor differences.
Port wing is S/No. 7352, stbd is 7284 (implying that the starboard wing is 78 units
earlier than the port wing. Airframe S/No is 7299. |
 |
My rather Heath-Robinson but effective wing
rotating jig on the butt end of the wing. |
 |
One of the two laminations that make up the
front spar has a splice installed at the factory. |
 |
Some of the holes where the fabric wire goes
through the ribs are slightly deformed, so I use a suitably-sized drill bit to bring them
back to the contour of the rib cap.
The cap has a depression along its length, to permit the wire to lie level with the
upper surface of the rib. |
 |
The ribs get the acid-etch and clean-up
treatment... |
 |
...and some of the two-sided ribs I have to
fettle and reinforce where previous knocks have dented them. |
Late June
 |
View of drill jig for opening out the existing
holes in the front spar. Using this jig, a hand-held drill can be used.
Behind the spar is a block of wood to drill into. The original bushings need
removing (pressing out with a drift) after alignment but before drilling.
Note that the root rib and first nose rib both need to be removed. |
 |
 |
The frame has five jig-bored 11/16" holes
at the correct spacing.
The frame holds two 11/16" diameter locating pins
which fit inside the existing 1/4" holes. As each hole is drilled, the locating pin
can be pushed in to the drilled hole.
An 11/16" diameter bush holds the Forstner bit.
The pins and bush are interchangeable in each hole of the frame to permit each of
the five spar holes to be opened out. |
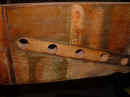 |
Here's the result...five aligned and parallel
bores in which to glue new bushings. |
 |
This is the comparison in diameter between the
old bushings (on the left) and new ones (on the right) - same size bolts though... |
 |
..and this photo shows the new bushings
installed dry in the bores. |
 |
I glue the bushings in, but to ensure final
alignment while the glue dries, I bolt up the new butt fittings. These fittings were
manufactured on the same DRO Bridgeport as the drilling jig, so I am confident of the fit.
The straps were ground on their faces over full length to ensure that they will fit
between the ears on the fuselage. |
July to August 2004
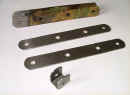 |
The new fittings for the rear spar; the
originals were severely corroded. |
 |
The end bracket is manufactured using a male
and female press die, with a drilling hole for the undersize hole (this to be reamed out
after welding). |
 |
 |
I use a wooden piece as a dummy spar to check
the assembly, which has an angled end. Note the pin used to ensure alignment of the
end hole... |
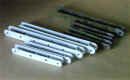 |
..and after welding & painting, here's the
result. |
 |
Spacers are used for the correct spacing of the
strut attachment brackets... |
 |
..and after welding of reinforcing plates. |
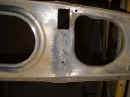 |
The butt ribs are severely corroded where they
butt up against the spars...requiring amputation of the cancerous bits...
[rectangular hole is aperture for spar butt fitting] |
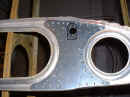 |
..and so needing some serious patches where
both front and rear spars meet the rib.
The reliance upon the Alclad to protect the material against moisture and wood acid
erosion was misplaced, perhaps in the light of what we know now.
Parts will be painted to protect them, before riveting together |
 |
More patches! |
 |
 |
Various wing internal components are bead
blasted and painted... |
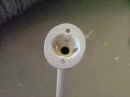 |
...and after painting, the internal bores are
treated with oil to prevent corrosion. |
 |
More painting! |
September 2004
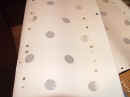 |
I completely de-riveted the aileron cove parts
(to get rid of more of those horrible steel rivets), and after cleaning up, re-fabricked
the inside of the cove. Flush solid rivets then installed in new holes to reattach
the stiffening edges. Pigeon Poo used during rivet installation (wet-riveting). |
 |
Previous problems with the last trailing edge
rib before the aileron bowing (because of fabric tension) will hopefully be resolved by
stiffening the rib with some 0.015" braces riveted on... |
 |
..and here is the result after screwing on the
other side of the rib, (braces fitted both top and bottom...space required between the two
braces for aileron cables). |
 |
Although I varnished all the holes through the
spars, you need to ream them out to fit the new bolts. Therefore there is always the risk
of the holes permitting bare wood and bare steel to come into contact (bad for corrosion).
So I use "Duralac" (Pigeon Poo) as a wet sealant immediately before
inserting the new bolts. |
 |
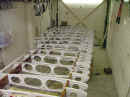 |
But wing reassembly is progressing!
(Drag wires go under anti-drag wires...but I am assembling inverted, so in my case,
they go the other way around).
Bare steel bolt heads will be wax-oiled for corrosion protection).
One of the compression struts is shorter than the rest; this goes at the strut
bracket fittings. |
October 2004
 |
 |
String lines assure the straightness of the
spars during trammelling. The right-hand photo shows the wing with a block inserted
under the front spar to simulate the wash-out to verify that nothing alters. |
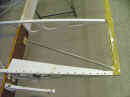 |
 |
The original Dahlstrom "C" section
used as bracing each end of the wing trailing edge were suffering a bit...so I am going to
replace them with stiffer and lighter aluminium tubing. Ali tubing annealed at the
ends using a light flame prior to bending/flattening. I used the more complete Dahlstrom pieces from the wing to make new ones for
the ailerons. |
 |
The leading and trailing edges undergo
necessary corrosion removal, repairs and fettling, prior to filling out the final few
dents with Poly-Fiber "Superfil". The blue slab is the wing, protected against
the up-and-coming overspray. |
 |
 |
Several iterations of paint/sand/fill,
paint/sand/fill were necessary. |
 |
So the port wing is structurally complete... |
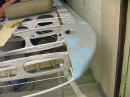 |
...well, almost. After turning over to
attach the underside of the leading edge, some more filling needed. |
 |
 |
 |
In the meantime, I have conducted cheque-book
aviation, and had a new nosebowl and lower cowl made by the local panel-beating shop.
16 gauge aluminium (thicker and stronger than original). Grilles
from Aircraft Spruce.
See Nosebowl Grille
fitting problems for why a new nosebowl is required.
The lower cowl is 2" oversize all round, so that I can do the final fit &
fettling in situ and get all the holes etc in the right place. |
November 2004: Ailerons
 |
 |
The ailerons themselves are in fair shape...a
bit of crushing on the attachment points, so new spars to be made. |
 |
 |
I designed a drilling jig to get all the
aileron spar holes in the right place. Sample piece of wood shows correct alignment. |
 |
Planing the new aileron spars. I modified
a cheap electric hand planer with longer blades to do the cut in one width. |
 |
I made a mess of measuring up the old spars, so
my new replacements need a lamination to get to the correct depth. Doh!
One can never have too many G-cramps. |
 |
Using aluminium foil as a wrap-around of the
timber load-bearing blocks when clamping up glued surfaces, prevents the glue sticking to
the blocks. |
 |
I am using aluminium reinforcing plates
(0.080") on the new aileron spars instead of plywood.
Floating anchor nuts will be used to permit any tightening of the bolts from the
front of the spars, eliminating the need for cutting a hole in the aileron fabric to get a
spanner on the nut. Using floating anchor nuts will ensure correct alignment of the
bolts.
The plates will be glued on, in order to eliminate the wood splitting with age
around the bolt holes. |
 |
Here is the result for the inboard bracket on
the rear wing spar(1).
Note also:
(2) I have not yet completed the final trammelling and lock-nut tightening on the
drag wires
(3) The aileron brackets still need attaching to the aileron cove with little
angles. |
 |
I can now drill the 3/16" holes in the
aileron spar using my jig. The depth of the jig allows me to free-hand the drilling; the
jig itself ensures alignment.
Some of the L2 drawings (on CD) were very useful in getting the correct dimensions
of the spar. |
 |
After varnishing, I temporarily mount the spar
to the wing brackets (to make sure it'll fit!) |
 |
The centre reinforcing plates are attached.
I am using a structural two-part adhesive. The purpose of the adhesive is not
to ensure attachment (the clamping of the through-bolts does this), but rather to bond the
wood to prevent longitudinal splitting of the spar where the holes pass through. I
also drilled 1 mm (0.040") diameter holes through the plates and nail through these
holes as per the drawing.
Note the use of tin foil to prevent the adhesive sticking to the wood backing
piece. |
 |
 |
 |
My friend David manufactured new aileron
brackets for me...and a jig to press them and drill them accurately.
A spot-welded piece on one side will prevent rotation of the pin in service.
Thanks, David, your skills and patience are very much appreciated. |
 |
I found it important to identify which rib came
from which location, to ensure that the screw holes match up between the metal parts. |
 |
 |
 |
After gluing on and nailing the outer two
attachment plates (after the ribs are slid on), another "dry run" ensures the
trailing edge lines up. I have increased the spar length by 1/4" each end to
reduce the enormous gap between the wing and the aileron ends. |
 |
The inboard end of the aileron gets a rib
reinforcing piece to prevent bowing under the fabric tension loads. This is a
one-piece "Vee-section" aluminium brace, countersunk riveted on to the aileron
butt rib AFTER the butt rib was nailed onto the spar.
Remember the round aluminium tubing used on the wing braces? Well, I cut the
corroded ends off the wing Dahlstrom pieces and re-used them in the ailerons. |
 |
I use my slip rolls to create a new tip leading
edge. The old one is Cleco'd to the new to get the right contour. |
December 04/Jan 05:
Wings (continued)
Much of the last month or two has been rebuilding
the structure of the starboard wing, so no real news to report, other than the following:
 |
 |
As per the port, the starboard wing spars
were varnished, and then masked off for spraying of the ribs (here in etch-prime).
Those components removed for rework were also etch-primed.
Two-pack epoxy prime to follow. |
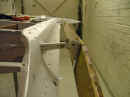 |
During rebuild of the aileron spars, I first
ensure alignment of the old aileron spars to the new aileron brackets. Then I can be
sure that the new aileron spars, when drilled according to the drawing, will fit. |
 |
Note that the lower edge of the aileron cove
(this photo taken while the wing is upside down) has drain holes for the lower section.
These must be allowed to ventilate to atmosphere.
The aileron cove was rid of the pesky steel rivets, and new flush rivets installed. |
 |
 |
Damage to the trailing edges of the wings and
ailerons is hammered out using a hardwood block, sanded to the correct contour.
Removal of rivets/staples holding the trailing edge is required, but with care, can be
reinstalled.
The final contour will be dressed with micro to get the proper shape. |
 |
The trailing edge of the starboard wing
contained the remnants of wasps nests...probably from Texas in the late Eighties. |
February 2005
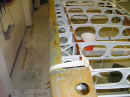 |
A trial re-fitting the leading edge. The
Cleco's fit rivet holes as found...there had evidently been previous damage to the wing
tip, necessitating replacement of the outboard leading edge. Note the truss rib
previously used as a replacement. This damage probably occurred in 1987, of
which I have heard anecdotal evidence, but no log book entry. |
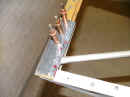 |
Some repair work required on the trailing edge
of the wing, due to corrosion of the original section. Note the round aluminium tube
used as bracing instead of the original Dahlstrom section. |
 |
After trammelling the wing, the starboard
aileron is jigged to the wing. I found it very valuable to do this while both the
wing and aileron were uncovered, since some shimming of the magnesium brackets (on the
wing rear spar) and of the aileron trailing edge were required to get the best alignment.
Note that I only dismantled the starboard aileron after rebuilding the port, so
that for both, I would have a pattern to work from. |
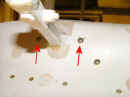 |
After final aileron jiggering and pokering, I
can secure the magnesium brackets to the cove. |
Go to page 1
2 3 4 5 6 7 8
Other
restoration photos
Taylorcraft.org.uk Home